LoneStar Fasteners Test Laboratory
LoneStar Fasteners recognize the necessity of rigorous testing processes
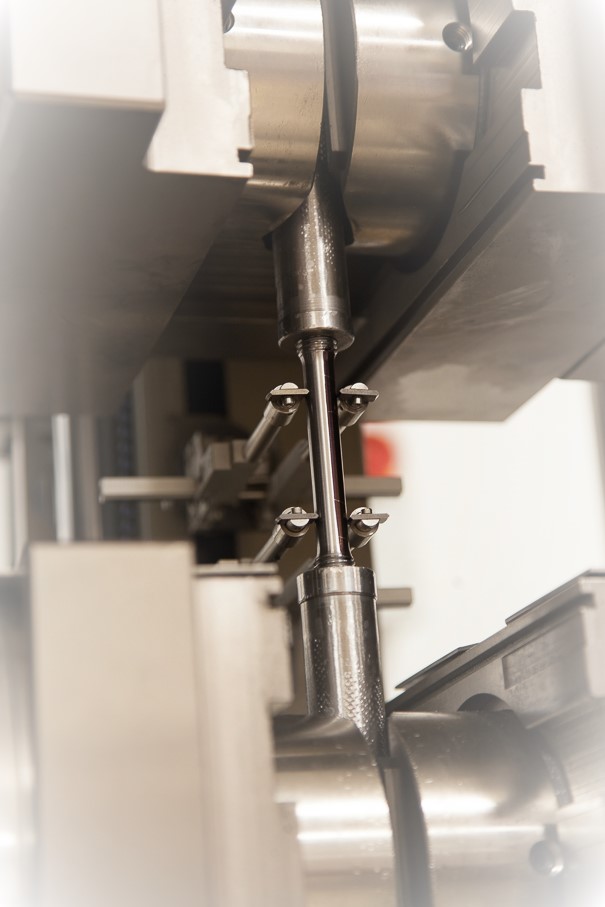
INTRODUCTION
LoneStar Fasteners recognize the necessity of rigorous testing processes
Delivering service excellence at LoneStar Fasteners has been the consistent heartbeat of the organisation, since it was founded in 1956.
Proving a market leading fasteners to the critical industries of oil & gas, automotive, construction, and heavy machinery has created growth in those services, whilst retaining a focus on precision and reliability.
Anticipating those customers’ needs, included the need for mechanical and metallurgical testing labs, to maintain our commitment to quality, and LoneStar Fasteners recognized the necessity of rigorous testing processes. From its inception, the company established an in-house mechanical testing lab to ensure that every product met the stringent standards required by its clients, which today is ISO 17025 accredited and sits within the Lonestar Global Test Laboratory network which serves customers with sites also in the Middle East and Europe.
Matching more complex customer requirements with investment and expansion in the laboratory’s capabilities. Metallurgical equipment with software analysis were key additions with two new Hitachi XRF analyzers, Salt Spray machine, new Rockwell hardness machines, magnaflux PT workstation, magnaflux horizontal mag bench along with an updated Tinius Olsen 300SL Universal tension testing machine, utilized for tensile and proof load tests. This was critical for verifying the strength and reliability of their fasteners. The development of a Non-Destructive Testing (NDT) ACCP Level II certification directly thru ASNT further enhanced the lab’s capabilities, allowing for the evaluation of surface and sub-surface cracks using techniques such as Magnetic Particle Testing, and Liquid Penetrant Testing.
Dedicated space was created to accommodate two precise metallurgical saws, high-resolution microscopes, and automatic polishers allowing for more efficient and accurate testing processes. The establishment of the metallurgical lab further demonstrates the company’s commitment to deepening its expertise in material science.
Today, the test laboratory facilities are extensive, covering a wide range of mechanical, PMI (positive material identification), coating inspection, NDT, and metallurgical tests. The mechanical lab is equipped with advanced hardness testers, Impact Tester, tensile testing machines, and environmental testing equipment. The NDT facility is capable of detecting surface and sub-surface defects using techniques such as Magnetic particle Examination & Liquid penetrant examination. Meanwhile, the metallurgical lab is operational, conducting crucial analyses such as coating evaluation, inclusion analysis and carburization/decarburization studies.
The team of qualified personnel are at the heart of the test laboratory’s service excellence and is staffed by highly qualified technicians. The team includes experienced personnel in mechanical & chemical testing, NDT inspectors with ASNT ACCP level II certification, and coating inspectors with NACE level certifications. These skilled professionals ensure that all tests are conducted to the highest standards, contributing to the company’s reputation for quality.
Latest News
Breaking ground on our forward momentum